Is a NR-311 Ni Electrode E70 Equal to a E80?

I have a project where we are welding ASTM A913-Grade 65 I-sections to each other. Our specification calls for E80 electrodes for these welds, in conformance with AWS D1.1. The steel erector submitted a WPS for these welds using NR-311 Ni electrodes. The WPS listed these electrodes as E80, thus we approved the WPS. However, the label on the weld wire box out in the field lists this electrode as E70, as does Lincoln Electric's literature on the electrode. When asked by the special inspector, the steel erector claimed that NR-311 Ni electrode is equal to an E80 even though it is technically listed as E70. They have submitted documentation, with Lincoln Electric letterhead, stating that the electrode is E70 but meets the requirements of E80. We are trying to determine if the electrode they are using meets the specifications, which specifically call for E80 electrodes. We're attempting to contact Lincoln Electric directly to get their opinion but we could use some outside advice, especially since the testing agency for the project seems reluctant to suggest anything and is looking to us for direction. Have you ever encountered a similar situation and if so how was it resolved? Please let me know what you would suggest.

Strictly
speaking, "E80" is not explicitly defined in any AWS document that I am aware of, although it
clearly suggests an 80ksi minimum UTS
electrode. If the specification did not specify a consumable
classification, then "matching" requirements for an ASTM A913, Grade
60 or 65 would be the classifications listed in AWS D1.1, Table 3.1, Group
III. These do not all start with "E80", although they are
nominally 80ksi minimum UTS. If the consumable manufacturer states in writing
that the particular electrode meets the properties of an E8XTX-X
classification, then the Engineer could accept it. I would not expect any
inspector or test lab to accept a classification unless it is shown as such on
the consumable manufacturer's literature or it was approved by the Engineer.
AWS A5.29-98 classifies the Lincoln NR-311 Ni electrode as E70T7-K2 indicating that it is has a minimum tensile strength of 70,000 psi. To add value to his or her service, the special inspector should have researched the contractors claim that this electrode met the requirements of the specifications. The special inspector, or his or her support personnel at the inspection agencys laboratory, should have gone to The Lincoln Electric Companys web site (www.lincolnelectric.com) and downloaded information for this electrode from the manufacturers catalog as well as the electrode Certificate of Conformance. Both of these documents indicate that the electrode meets the requirements of the specifications, 80,000 psi minimum tensile strength, as well as FEMA 353 requirements. These documents then should have been forwarded to the EOR for review, and either approval or rejection.
NDT of Fillet Welds?

What NDT inspection criteria is required by code for fillet welds?
There
are no general requirements for NDT of fillet welds in the 2001 CBC, AWS D1.1,
AWS D1.8, or the AISC Specifications. The requirements in CBC Section 1703
apply only to the welds noted, and are the minimum NDT requirements. The
Engineer has the option of requiring testing beyond the minimum requirements,
including NDT of fillet welds, as part of the Statement of Special Inspections
prepared by the responsible design professional. However, such testing is not
specifically required by code.
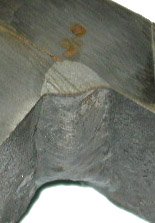
Appendix Q of the
2005 AISC Seismic Provisions for
Structural Steel Buildings (AISC 341) now lists specific locations where
NDT is required for connections resisting seismic forces. The only connections
that could potentially involve fillet welds are welds within the
"k-area" of the section and repairs within the plastic hinge region
of reduced beam section (RBS) moment frame connections. These provisions have
not yet been adopted into the California Building Code.
FEMA-353
recommends the Engineer to develop a Quality Assurance Plan and indicate the
appropriate Seismic Weld Demand Category and Seismic Weld Consequence Category
for each welded joint on the design drawings. Magnetic particle testing
is specified for fillet and PJP welds in all but two categories.
If desired, Magnetic Particle Testing (MT) should be
used to test fillet welds. Ultrasonic Testing (UT) should not be specified for
fillet welds.
Is an Overhead Puddle Weld Possible?
I have specified a overhead puddle weld on a
project and the contractor is claiming that they cannot perform this weld. Im
attempting to determine if the contractor is correct. Do you have any thoughts
on this?
Puddle welds are typically
used to join sheet metal to underlying
structural steel elements. These welds
are generally completed by using high heat settings to allow for burning
through of the sheet metal. With the
higher heat required for this welding technique a larger weld puddle is formed
than would typically be created with the use of a lower heat (amperage)
setting. The connection strength of the
puddle metal is a function of the perimeter area of the weld. With the larger puddle area of a puddle weld
versus that of a linear weld or plug weld, and the higher heat of the molten
metal, the application of a puddle weld is governed by gravity. The forces of gravity do not allow for the
creation of a larger weld puddle as is common for a puddle weld in any position
other than the flat position.
The completion of welds on a vertical surface and in
the overhead position requires a much greater degree of control on the heat
settings so that sufficient heat is applied to obtain proper penetration while
excessive heat is avoided. This does not
allow for burning through of the sheet metal to create the weld. By avoiding the overheating of the metals
the molten metals will freeze much quicker and the effects of gravity are
overcome. By designating a plug weld as
opposed to a puddle weld a hole of the required size (perimeter) is provided in
the sheet metal prior to the start of welding.
The weld is then made along the perimeter of the hole using a lower heat
setting that provides for proper penetration while controlling the size of the
weld puddle to avoid loss of metal due to drop out associated with gravity.
Where the interior of the hole is to be completely filled with weld metal a
plug is created that can be ground and dressed to create a uniform surface with
that of the surrounding metal.
Arc spot (puddle) welds and arc seam welds are only
done in the flat position. See AWS D1.3-98, Table 1.2 It is almost impossible
to do them in any other position.
The simple answer is that if the contractor wont do
it, its not going to get done - regardless of theory.
See D1.3-98 Table 4.1 for standard joints. #4.4, Arc
spot weld-sheet to supporting structural member is only shown for F, i.e., flat
weld only. #4.5B is only shown for the Horizontal position.
The relevant all-position weld might be #4.5, the
arc plug weld.
UT Acceptance Criteria, FEME-353 VS AWS D1.1

I need some advice on the UT acceptance criteria for
CJP welds. The welding inspector for the project that Im working on claims
that the acceptance criteria specified in AWS D1.1 differs from that specified
in FEMA353, and he is asking us to specify which criteria they should use. Our
project uses special moment resisting frames, so the welds at the connections
and the column splices are critical elements. The project specifications state
the following: Ultrasonic testing (UT)
shall be conducted by the Owners Testing Agency for the percentage of joints
designated in Table 2-1. UT shall be performed in accordance with AWS D1.1.
FEMA-353 is cited elsewhere in the specifications but not in regards to UT. I
looked at AWS D1.1 and cannot determine if or how it differs from FEMA353. I
also reviewed AWS D1.8 and it appears to match FEMA-353 and thus adds to my
confusion.
What concerns me about the specification is that Im
sure that the differences between AWS D1.1 and FEMA-353/D1.8 were not taken
into account when the provision was written. Thats why I need the
clarification. Should we be using D1.8 or D1.1 or both?

AWS D1.1 has two ultrasonic testing
procedures and acceptance criteria.
The primary one,
used for decades and most commonly accepted, is contained in Section 6, Part F. Annex K,
referenced in FEMA 353, UT Examination of
Welds by Alternate Techniques, is relatively new.
Since FEMA-353 was not specified for
ultrasonic testing in the project documents, AWS D1.1, Section 6, Part F would
be the procedure to be used. Some
reasons for this are as follows: FEMA-353, Section
5.8.3 allows the engineer the option of either AWS D1.1 Annex K or Table 6.2
(Section 6, Part F). Annex K (moved to
Annex S in 2006), states, This annex is non-mandatory unless specified in the
contract documents. AISC 341s1-05 and
AWS D1.8-06 specify AWS D1.1, Section 6, Part F unless alternative procedures
are approved by the engineer.
If given the choice, I prefer
the D1.1 criteria, primarily because there are precious few UT technicians that
can accurately and reliably size flaws in 3 dimensions. As the welding
inspector suggests, in his original request, the FEMA-353 criteria may not be
as conservative as D1.1, particularly considering the lower probability of
detection and accuracy of sizing for technicians whose experience is
predominantly with the D1.1, Sec. 6, Parts C & F criteria and methods.
What Variations can be Developed from a WPS?
 Does
a PQR for a butt joint qualify a WPS for a T or corner joint with the same weld
size?
Also, does a PQR for a groove weld qualify a
WPS for a fillet weld of the same size?

Yes, WPS qualification of a
complete joint penetration (CJP) groove weld (butt joint) qualifies tee and
corner (CJP & PJP) joints within the limits of the qualified WPS, it also
qualifies fillet welds within the limits of AWS D1.1 Table 4.1 & 4.2 Note
4. Most fillet welds are afforded pre-qualified status per AWS D1.1 Section 3.9.
When responding to frequently asked
questions, the apparent code answer is not always what the inquirer may be
seeking. When reviewing and approving
welding procedure specifications, the Engineer has the authority to relax
code requirements or enforce more stringent requirements. In this case, it is possible that the project
team was looking for a more comprehensive analysis due to a critical connection
required by their design. Following is an interpretation of the code with that thought
in mind.1. For a complete joint penetration (CJP) groove weld, at first glance, yes. AWS D1.1-06, Section 4.9.1.1 Corner or T-Joints states Test specimens for groove welds in corner or T-joints shall be butt joints having the same groove configuration as the corner or T-joint to be used on construction
.
However, AWS D1.1-06, Table 4.3, Note 2. states If a PJP bevel- or J-groove weld is to be used for T-joints or double-bevel- or double-J-groove weld is to be used for corner joints, the butt joint shall have a temporary restrictive plate in the plane of the square face to simulate a T-joint configuration. Welding Procedure Specifications (WPSs) requiring qualification by test, resulting in Performance Qualification Test Records (PQRs), are typically done to qualify an unproven joint configuration, base metal, weld metal combination. The ability of a/any welder to accomplish a sound weld during construction using this type of WPS is very important. It is recommended that WPSs that are not pre-qualified for T-joints and/or corner joints with J-grooves or double-bevel groove or double-J-groove, whether CJP or PJP, be qualified using a temporary restrictive plate, prior to approval by the Engineer. 2. Yes.
AWS D1.1-06, Table 4.2, Note 4. states CJP groove weld qualification on any thickness or diameter shall
qualify any size fillet or PJP groove weld for any thickness.
Are Ceramic Back-ups Prequalified?
 Upon partial completion of a project the project
manager rejected one of the WPSs used.
The contractor had used an AWS prequalified TC-U4a-GF joint
configuration that by code requires metal backing. But, the contractor used
ceramic backing. He removed the ceramic
backing, back-gouged and welded the root. Is there any way that this might be considered acceptable?

Answer: Possibly.
AWS D1.1 - 2.17 Prohibited Joints and Welds
2.17.1
One-Sided Groove Welds. Groove
welds, made from one side only without backing or made with backing, other than
steel, that has not been qualified in conformance with Section 4 shall be
prohibited
We arent taking about One-Sided Groove Welds, so this
restriction does not apply. In an attempt to mitigate this situation, from an administrative
point of view, we designate the prequalified joint configuration to be
TCU4b-GF, similar to the TC-U4a-GF joint configuration.
Next, we look at D1.1 - Fabrication. We cannot prohibit the
contractor from using his own methods and means to produce welds, as long as
they are within the limitations of the code. The contractor uses the TC-U4b-GF joint configuration, elects to
use the widest As Fit-Up root opening allowed, uses ceramic backing, and
cites the following:
AWS D1.1 - 5.10 Backing
Roots of groove
or fillet welds may be backed by copper, flux, glass tape, ceramic, iron
powder, or similar materials to prevent melting through.
Since the weld is to be back-gouged and welded, as an inspector, I
would have to allow this, verifying that the groove angle was within the
tolerances of the 45º bevel preparation and not the 30º that may be used in the
case of the TC-U4a-GF joint configuration.
(After back-gouging, the other side of partially welded joints
should resemble a prequalified U- or J-joint configuration at the joint
root, and, for administrative purposes, would require an additional WPS.) |