Newsletter
The TEI Newsletter Number 12, September 23, 2005 By: Dan Watanabe
INTRODUCTION There are three broad divisions within civil engineering into which applications of FRP can be classified: new construction, architectural applications, and repair and rehabilitation. FRPs have been used widely by civil engineers in the design of new structures. Bridges and columns built completely out of FRP composites have demonstrated exceptional durability, and effective resistance to effects of environmental exposure. Pre-stressing tendons, dowels, reinforcing bars, blast mitigation and grid reinforcement are all examples of the many diverse applications of FRP in new structures. Architects have also discovered the many applications for which FRP can be used. These include structural sub-systems such as siding/cladding, roofing, flooring and partitions. One of the most common uses of FRP involves the repair and rehabilitation of damaged or deteriorating structures. Several companies across the world are beginning to wrap damaged bridge piers to prevent collapse, improve the structural integrity of steel-reinforced columns to and to prevent buckling of the reinforcement. Recent earthquakes in urban areas such as Loma Prieta ’89, Northridge’94 and Kobe’95, have repeatedly demonstrated the vulnerabilities of older reinforced concrete columns to seismic deformation demands. Particularly vulnerable are bridge piers designed prior to the 1971 San Fernando earthquake. Before that time the transverse or horizontal column reinforcement was only nominally provided, typically #4 bars spaced 12 in. on center, independent of column size, strength or deformation demands.
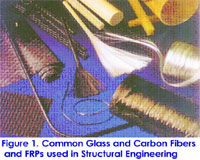 FRP Laminate Structure FRPs are typically organized in a laminate structure, such that each lamina (or flat layer) contains an arrangement of unidirectional fibers or woven fibers fabrics embedded within a thin layer of light polymer matrix material. The fibers, typically composed of carbon or glass, provide the strength and stiffness. Glass fibers are the most common materials accounting for approximately 90% of all fibers used. The matrix, often made of polyester, Epoxy or Nylon, binds and protects the fibers from damage, and transfers the stresses between fibers.
TEI’s Role TEI is constantly trying to identify and enter new markets and to that effect we have acquired laboratory (AC 17025) and auditing (AC 17020) accreditation from the International Accreditation Service (IAS), formerly ICBO ES. Armed with these credentials we have pursued projects with FRP installation and audits of FRP manufactures. TEI has performed field inspection, testing and laboratory testing (AC178) on several FRP installation projects such as Fort Mason, Mechanics Bank and Cache Creek Casino. TEI also performs services for other testing and inspection companies such as Signet, CTS and HVJ Associates. We have an established working relationship with the Fife Company, manufactures of TYFO® Fibrwrap® one of the largest manufacturers and installers of FRP. We are also the Quality Control agency for Edge Structural Composites, where we perform quarterly Q.C. audits for the International Code Council (ICC) product approval.
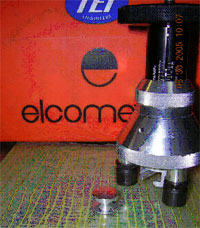 Field inspection (AC178) typically consists of, but is not limited to verification of installer certification, material verification, product storage, epoxy mixing, surface preparation, fiber orientation, and placement. Installation projects are required to make two 12” x 12” test panels per day one in the morning and one in the afternoon. Field testing may vary with different projects, but the most common tests are Durameter readings, where relative hardness measurements are taken at specified intervals to ensure proper epoxy/resin cure rate. Adhesion testing (ASTM D4541) is performed with an elcometer, where pucks are glued on the face of the FRP and cored around the puck to the substrata. The puck is then pulled off and the adhesion strength determined. After the FRP has been installed and cured a sounding test is performed, where tapping the FRP with a small hammer is used to determine debond areas by the resulting sound.
Laboratory testing associated with field installation performance testing is performed on the 12” x 12” test panel fabricated at the project. Once the panels are submitted to our laboratory they are cured in an oven at 120 deg. F for 24 hours. Upon removal from the oven, 1” wide coupons are removed along the primary fiber direction, tabs are glue to each end of the coupons and allowed to cure for 24 hours, and the samples tensile tested. The tabs are glued on to prevent localized crushing and aid with the transfer of stresses to the fibers. The most common problem is low tensile strength results due to fiber alignment. When there are two layers of fiber it is critical that the fibers from each layer align parallel with each other.
Current Research on FRP A serious concern relating to the use of FRPs in civil applications is the lack of design codes and specifications. For nearly a decade now, researchers from China, Europe, and Japan have been collaborating in hopes of developing such documents to provide guidance for engineers designing FRP structures. The advent of design codes and specifications will increase awareness of FRP and therefore increase its use. Increased use will mean more testing and inspection opportunities for TEI.
|